Key Markets served - We ship worldwide.....Buy Magnets here
- Defense & Aerospace
- Automotive & Medical
- Equipment Builders
- Food, Feed, Grain, Paper & Pulp
- Manufacturing & Processing Industries
- Metalworking Processors, Machining & Grinding, Stamping, Cold Heading & Fabricating
- OEM’s, Automation & Robotics
- Office Equipment & Metal Components
- Petroleum & Chemicals
- Plastics Processing
- Recycling - All Industries
- R & D Custom Magnets & Precision Metal Fabrications
- Transportation & Automotive....
Alnico Magnets / Alnico Bar Magnets
Alnico magnets are a type of permanent magnet that is manufactured from a specific magnetic alloy for the properties that it contains. The magnetic alloy, “alnico,” is an acronym of aluminum, nickel and cobalt, the three main elements in this mid-grade permanent magnet. Some characteristics of alnico are that it is hard, brittle, has a low coercive force, excellent temperature stability, high residual induction and fairly high energies.
Alnico magnets, in addition to their composition of aluminum, nickel and cobalt, can also be alloyed with iron, copper and often titanium in order to create a magnet with a stronger magnetic force than all other permanent magnets (with the exception of the rare earth elements of neodymium and samarium-cobalt).
More cost-effective than high-strength rare earth magnets and having higher magnetic force and permanence than ceramic magnets, alnico magnets are the perfect fit for a wide range of applications. For instance, cow magnets are made exclusively from alnico, and alnico magnets are also used in sound amplification, electric motors, sensors and many sorting and lifting tools.
In addition to these applications, alnico magnets are utilized in industries including instrumentation, research and music for electric guitar pickups, loudspeakers, traveling wave tubes and many others.
Alnico magnets are similar to ferrite ceramic magnets but are less brittle, more easily fabricated into shapes, and have higher magnetic resistance. Being a metallic magnet rather than ceramic, they do not need always to be nickel-coated for structural applications like ceramic magnets do.
Additionally, alnico magnets have medium-high magnetic force but relatively unstable magnetic permanence under corrosion or vibration, making them unsuitable for motor, water treatment and sound speaker applications. There are two main methods by which alnico magnets are fabricated: casting and sintering processes.
The casting process entails heating up the alnico until it achieves a molten state, and then pouring the molten alnico into a mold. Once in the mold, the alnico is further processed by means of varied heat treating cycles. Cast alnico magnets offer the advantage of working extremely well in terms of magnetic capability, but suffer in terms of mechanical properties as they are often characterized by casting voids and hairlines cracks in the alnico.
The sintering process, on the other hand, involves the manufacturing of solid parts, such as various stock magnet shapes like rods, bars, channels and horseshoes, from powdered materials that are heated to just below the melting point in order to cause particulate adhesion.
Bar Magnets / Samarium Cobalt Bar, Ring, and Disc Magnets
Bar magnets are narrow, rectangular pieces of ferromagnetic material or composite that generate a magnetic field. They are permanent magnets, meaning they do not require constant electric current in order to retain their magnetism, and they have a smooth and uniform cross section and surface. They are usually made from iron or steel, but they can also be made from any ferromagnetic substance or composite such as cobalt, nickel, aluminum or clay.
Bar magnets have a south and north pole on each end and are the most common type of magnet shape. The main function of bar magnets is to to pick up small metallic objects like metal shavings or nails and screws, as magnetic stirring rods in laboratory applications, and as magnets on refrigerators. Their most common application is the needle used in compasses.
The north pole of the bar magnet aligns with the actual north pole, letting travelers know in what direction they are headed. However, this is not the only application of bar magnets, which are utilized in a wide range of industries and applications including: residential, for applications such as holding up receipts and pictures onto refrigerators; research, in which they are used as stirring rods on laboratory hotplates; and the food industry, utilized in restaurants to hold the cutlery in an organized and safe location.
The magnetic lines of force of a bar magnet form closed, continuous lines on either side of the magnet. They never intersect, and flow from north to south in direction. Each end of the magnet is considered to be a pole, so when cut in half a bar magnet automatically forms into two separate magnets, each with their own poles and magnetic field.
The average magnetization magnitude of bar magnets is 100,000 A/m, but this varies based on what type of ferromagnetic material is chosen. In addition, the magnitude of the magnetism relates to how strong and far apart the two poles of the bar magnet are. When using any type of magnet, especially bar magnets that are often found in homes, it is important to keep them away from any sort of electronic device, including speakers, televisions and radios.
Irreversible damage can occur to the data storage if it comes in contact with a magnet, even if it has a weak magnetic force. While the most obvious function of a bar magnet is to attract iron or ferromagnetic materials, bar magnets also function to attract or repel other magnetic alloys. These magnetic alloys include nickel, cobalt, some rare Earth metals and their alloys, and some naturally occurring minerals such as lodestone.
Bonded Magnets / Bonded SmCo, Ferrite, and Neodymium Magnets
Magnets are products that come in a number of shapes and sizes, and the magnets that have really pushed the mold have been bonded magnets. These magnets combine thermoplastic and thermoelastomer resins with magnetic powders in order to create injection molded, flexible magnets. These magnets are great for custom applications where a traditional, solid magnet would not offer the same type of value.
Injection molding is not the only process in which bonded magnets are created as bonded magnet manufacturers also utilize the compression bonding process in order to supply customers with a higher magnetic output. The trade-off between the two being that while compression bonded magnets offer a higher magnetic output, they are limited in the shape and sizes whereas injection molded magnets are rather flexible.
These bonded magnets are great for a wide range of applications from sensors to brushless DC motors and just about everything else in between. The two different processes used to create the bonded magnets, injection molding and compression bonding, yield different characteristics when it comes to their final product.
For example, a bonded magnets that is manufactured through the injection molding process has a very high mechanical strength, meaning it has a high tensile strength or that it can withstand a great amount of physical force. Compression bonded magnets on the other hand yield only a moderate amount of mechanical strength, but keep in mind that compression bonded magnets offer higher magnetic strength which can be attributed to their higher magnetic particle density.
There are many options when searching for the right type of bonded magnet for your application and a lot of factors to consider when making that choice. The type of applications and your requirements are the most important to consider. Ask yourself questions such as: Will the magnet be exposed to extreme temperatures? Will the magnet be exposed to solvents or outside fluids? Can my application fit a traditional style magnet or do I require a more flexible solution?
All of these questions are a great start to finding the perfect bonded magnet solution. Once you know what you are looking for, finding a trusted bonded magnet manufacturer is the next step in the process. They can help you fine tune your selection in order to better fit your application and will ensure that you receive the best possible bonded magnet based on your needs and requirements.
Ceramic Magnets / Ceramic Block, Ring, and Disc Magnets
Ceramic magnets, or ferrite magnets, are the most common magnet used in industrial applications. As permanent magnets, ceramic magnets have a much stronger magnetic force than most other common magnets, and their non-metallic ceramic composition makes them the most affordable magnet capable of industrial strength magnetic force.
As their name implies, ceramic magnets are a sintered composite of powdered iron oxide, strontium (or barium) and ceramic powder; the finished product is a brittle and porous charcoal gray ceramic. As a result of their brittle, porous composition, ceramic magnets are often nickel coated to prevent chipping and breaking.
As with powdered metal parts, ceramic magnets can be compacted into blocks, discs and arcs while in powdered form. Once the magnet is sintered, however, machining and forming can be difficult and costly; due to their brittleness and hardness, diamond cutters are usually required to machine ceramic magnets.
Although the magnetic force of ceramic magnets is ranked slightly below alnico magnets (a metallic magnet composited from aluminum, nickel and cobalt) and much lower than rare earth magnets, ceramic magnets are prized not only for their cost economy but also for their magnetic permanence.
One of the most important aspects of a magnet’s ability to retain its magnetism under corrosion, vibration, exposure to electrical fields, time and heat is important because it determines for which applications a magnet may be used. Ceramic magnets have excellent magnetic permanence under corrosion and electrical exposure, making them the perfect material for DC motors, speakers and lifting, retrieving and separating corrosive materials.
In addition, ceramic magnets’ magnetic permanence is beneficial in the welding and construction industries as well as other motor, sound and electromagnetic environments subject to vibration and electricity, but their thermal stability is very poor. Applications which require industrial-strength magnets to operate under high heat use either alnico magnets, which maintain magnetic permanence at up to 550 degrees Celsius, or samarium cobalt rare earth magnets, which also have excellent high heat resistance.
Some examples of applications that ceramic magnets are found in many home appliances, automobiles, children’s toys, tools and equipment at the doctor’s office. In addition, ceramic magnets are often found in refrigerator magnet hooks, and they are notably stronger than other refrigerator sheet magnets’ poly-magnetic compounds.
Electromagnets
An electromagnet is a type of magnet that is composed of a battery and iron wire that uses electric current in order to generate a magnetic field.
The magnetic field is generated when the electric current passes through a wire, and the field dissipates when the current stops. The primary function of electromagnets is that they are used to lift metallic objects as well as being utilized in the design of many different machines and electronic systems.
Scientific laboratories, manufacturing plants that handle scrap metal, the automotive industry and appliance and electronic manufacturers all benefit from the use of electromagnets. In addition, they are part of the design of electric motors, generators, doorbells, circuit breakers, TVs, speakers and read and write heads for hard disks and tape drives.
In the automotive industry, electromagnets are used to manufacture brakes and clutches in vehicles. In factories and plants, electromagnets are used to lift and suspend scrap metal and other heavy metallic objects like billets, steel plates, bars and forgings. In many of these applications a permanent magnet can be used instead of an electromagnet; however, electromagnets offer the advantage of being able to manipulate the magnetic field over a wide range at a rapid pace.
There are a few main components that are utilized in the formation of electromagnets: a battery and an iron wire. This wire is often formed into a coil, and can be formed into various shapes including that of a helix, making it a solenoid coil and that of a donut-shape, making it a toroid coil.
In addition, the material of iron is used as the wire component in electromagnets because it belongs to a small group of metals that exhibit ferromagnetic properties and generates a magnetic field when exposed to an electrical current. The magnetism only exists when current is flowing from the battery. This type of soft iron core is also referred to as a ferromagnetic core and offers extremely high magnetic permeability. There are two main types of electromagnets.
The first, flat-fraud, is mainly used when the magnet is able to attach itself to a smooth, flat piece of metal. Parallel-pole electromagnets have two poles spaced far apart from each other that allow the magnetic field to have a greater reach. These are used when the metallic object is of an irregular shape and only comes in partial contact with the magnet surface.
Ferrite Magnets / Flexible and Sintered Ferrite Magnets
When you think of magnets, ferrite magnets are probably what you think of first because they are the most common and most affordable type of magnets. Not to mention that they are heavily involved in children’s toys and television shows.
A ferrite magnet is made up of two chemical compounds magnetite and hematite, magnetite is actually the most naturally occurring magnetic mineral found on the planet which is why ferrite magnets are so affordable. There are a number of different categories and ways to categorize ferrite magnets, so it is best to know what you are looking for before purchasing or to consult with an experienced ferrite magnet manufacturer.
In general, ferrite magnets are put into two different categories, soft ferrites and hard ferrites. In order to categorize them, their magnetic coercivity (persistence of internal magnetism) is evaluated. Unlike most substances, hard and soft has nothing to do with the brittleness of the magnet as both categories are rather brittle. Instead, it has to do with the amount of coercive force the magnet produces. Because this kind of magnet can be split into these two categories, they are incredibly versatile and can be found in many different applications and industries.
Each type is ideally suited for different applications. For example, you might find a hard ferrite magnet within a hard disk drive or radio due to the greater amount of coercive force needed, while on the other hand, a soft ferrite magnet is would more likely be used in applications like electromagnetic cores or transformer cores where coercive force is not as important.
So while a ferrite magnet may be far simpler than an alnico or neodymium magnet, it is important to know that there are still a number of options and factors to consider. This is why it is so crucial to find a trusted, experienced ferrite magnet manufacturer, ensuring that you receive the best possible solution for your unique applications.
Flexible Magnets
Magnets are products that serve a wide range of functions and applications, because of this they are found in a wide range of industries as well. Pretty much all magnets operate in the same way, yet there are a few different designs, materials, and styles to choose from when searching for a magnet.
Flexible magnets are perhaps some of the most interesting magnets on the market. As their name suggests, these magnets are flexible, meaning that they have the ability to be bent and manipulated in order to fit a specific application or use. In addition to this, flexible magnets also have the ability to be cut to virtually any shape desired which makes them the go to magnet for custom applications.
Flexible magnets are found in a number of different industries from manufacturing applications to use in schools, homes and many forms of business. They are found in such a variety of applications and industries because of their ability to be shaped and manipulated, both during and after the manufacturing phase, to fit a specific requirement.
Flexible magnets are typically formed through two different processes, extrusion or calendaring. Deciding between the two different manufacturing processes depends mostly on how the magnet will be cut or manipulated later on in its use. Extrusion is done by squeezing the magnetic material into a mold where it is allowed to cool, forming thin magnetic strips. On the other hand, calendaring is a process in which a magnetic compound is passed through a roller until a magnetic sheet is formed.
The thickness of the magnetic sheet can be manipulated based on the number of times it is passed through the roller. Once the magnetic sheet or strip is completed the cutting can begin. Obviously, if you require a larger flexible magnet, then calendaring may better suit your needs, since it allows you to cut from the larger sheet of magnetic compound rather than the strips that are created through the extrusion process. That being said, the extrusion process is the much preferred method due to its accuracy and efficiency when it comes to flexible magnets.
While flexible magnets offer a number of unique advantages over the more traditional, solid magnets, they are also less durable which makes them a liability in certain applications. The best way to ensure that you receive reliable, flexible magnets is to find a trusted and experienced flexible magnet manufacturer who is able to listen to your application in order to suggest the right solution for you and your applications.
Industrial Magnets
Industrial magnets are high-strength magnets that have certain characteristics that make them ideal for applications in the industrial industry. In general, a wide spectrum of industries are increasingly using high-strength magnets to do all kinds of work, from physical metal lifting and separating to motor activation and Magnetic Resonance Imaging (MRI).
Different applications require different types of industrial magnets. Industrial magnets can be broken up into two main categories: non-permanent and permanent. Non-permanent magnets are electromagnets which require an outside electric current to be magnetized or demagnetized. Permanent magnets include ceramic magnets (also known as ferrite magnets), alnico magnets and rare earth magnets.
Ceramic magnets have lower magnetic power and are more brittle and easily breakable than some other magnets, but they are cost-effective and retain magnetism under corrosion and vibration. Rare earth magnets are less cost-effective to manufacture but are far more powerful and retain their magnetism better than ferrite magnets.
Neodymium magnets are the strongest and most commonly used industrial rare earth magnet; sheet magnets are made from a flexible ferrite-plastic composite which is extruded into sheets and used in automotive and consumer industries.
There are many different types of magnetic materials that industrial magnets can be fabricated from. The most important properties magnet manufacturers consider during fabrication are porosity; ease of fabrication; magnetic retention (or magnetic permanence) under heat, corrosion and vibration; magnetic strength; and cost.
Types of permanent magnets are made from different composites and therefore have very different properties and applications. For instance, ceramic and alnico magnets are most often used for physical lifting and separating. Magnetic tools which do this kind of work often contain multiple magnets in specific configurations called magnetic assemblies.
Lifting, holding and separating magnetic assemblies are used in metal fabricating, construction, engineering, automotive, electronic, water treatment and agricultural industries among others. Arc-shaped ceramic magnets are often used in motors, and most stereo speakers use ceramic magnet discs.
Rare earth magnets and magnet assemblies have much stronger magnetic fields than ceramic or alnico magnets and are used in sensitive electric motor, computer hard drive, TV monitor, sensor and medical applications. Electromagnets are used by automotive, medical, metal fabrication and aerospace industries in applications such as solenoid valves, AC and DC motors, biomagnetic separation, beam control, transformers and car crushing.
Magnetic Separators / Magnets
Magnetic separators can utilize both permanent magnets and electromagnets which is used to separate ferrous materials from nonferrous materials.These items are ideal in manufacturing settings where metallic materials must be extracted to purify the process stream as well as for recycling applications.
In many industrial applications, materials can be passed through, below, or over magnetic separators. The magnets attract the impurities within the material of interest and pull out this unwanted matter. Thus the process stream is purified of undesired material.
This kind of equipment is used in a number of industries, including the electronic waste recycling, materials recovery, municipal solid waste/biomass, bottom ash, construction, demolition, and glass cullet industries as well as many others.
Magnetic separators also come in a wide range of configurations such as plate magnets, grate magnets, liquid line trap magnets, RF cartridges, deep reach separators, pulley magnets, magnetic drums, suspended permanent magnets, super conducting hi-gradient magnetic separators and much more.
Specific types of magnetic separators can be specialized for different tasks based upon the exact needs of an application which is where high intensity magnetic separators and eddy current separators play a role.
Magnetic Strips
Magnetic strips are thin pieces of flexible magnetic rubber material that usually have an adhesive on one side and can conform to irregular or uneven surfaces that are magnetically receptive. The ability to conform to uneven surfaces is advantageous for many industries and applications in which heavy working and corrosive environments cause surface elements to deteriorate and lose their initial even perfection over time.
Magnetic strips are the most inexpensive type of magnetic shape and are typically manufactured from a mixture of ferrite magnet powder and rubber material, and are undergoing further forming by means of the extrusion process.
These flexible strips come in large rolls and are used for a wide range of applications, particularly residential and commercial applications such as signs, refrigerator magnets, POP displays, craft supplies, trade show displays, markers and advertising boards.
Also used for industrial applications such as in switches, manufactured products and sensory devices, magnetic strips provide noise and vibration dampening. In addition, magnetic strips are commonly utilized in sealing applications as well. For instance, latching, gaskets, door seals, shower and bathroom sealing and refrigerator door sealing are all accomplished with the use of magnetic rubber strips.
Magnetic strip are almost always manufactured with some sort of adhesive backing in order to better conform to the desired surface. Some common materials used for the adhesive backings on magnetic strips are acrylic-based adhesives, normal and foam, and rubber-based adhesives, craft, high-track and foam. The physical appearance of most basic strips of magnetic rubber is uncoated and a dark brown color.
However, magnetic strips can be laminated on the non-magnetic side of the strip. In addition, they all have a weak and strong magnetic side, are cut easily, lightweight, are permanent magnets and, therefore, are reusable. For standard sizes of magnetic strips, their width ranges from .5 to 2 inches, while their thickness is anywhere from .03 to 1 inch thick.
The most common thickness of magnetic strips is .6 inches, which provides enough strength for most strip applications. The adhesive backing may be foam or a pressure-sensitive backing material, that is rubber-based for indoor and craft applications, or acrylic-based, which adheres to plastics and vinyl for both indoor and outdoor uses.
Some magnetic strips have a vinyl outer coating, which provides a wide range of color options. Steel backing also provides more bonding strength.
Neodymium Magnets / Magnets
Neodymium magnets are fabricated from neodymium, which is an element with the physical characteristics of a soft, silvery metal. This material is also characterized by being one of the more reactive rare earth elements, which are a collection of seventeen chemical elements found in the periodic table. For applications which require exceptionally strong magnets, rare earth magnets are by far the most effective.
Out of all rare earth magnets, neodymium magnets are by far the strongest type of magnet. In addition, Neodymium magnets in particular offer the best value when comparing performance, size and cost. Fabricated from a compound of neodymium, iron and boron, neodymium magnets, like all rare earth magnets, have a much greater magnetic strength to size ratio than other types of magnets, and they have excellent resistance to demagnetization.
Although the manufacturing process can be costlier than for other magnets, neo magnets require far less volume than non-rare earth magnets. Like ceramic magnets, neodymium magnets are first made into a powder then pressed into shapes. After a magnetic field is applied to orient the soon-to-be magnet, neo magnets are sintered until they are fully dense. This process can yield neodymium magnets in a variety of shapes.
Neodymium magnets are both stronger and more affordable than samarium cobalt magnets and are therefore more widely used for most applications. Magnetic permanence under conditions such as vibration, corrosion, electric fields and heat is a crucial factor for magnets used in industrial, automotive and medical equipment, and although neodymium composites have great magnetic force, they easily lose their magnetism under corrosion and relatively low temperatures (200 degrees Celsius).
They are also easily chipped or cracked and are therefore almost always given a protective nickel or other metal coating. Samarium magnets, which have good high heat tolerance, are used where neodymium magnets’ heat tolerance is too low. In terms of applications of neodymium magnets, as the automotive and energy industries explore petroleum alternatives, the rare earth magnet industry has seen a sharp rise.
Neodymium magnets are crucial in most electric motors and wind turbines, and concern has already been raised regarding lanthanoid ore shortages. However, medical, aerospace, electronics and automotive industries have barely begun to harness the natural power of rare earth magnets. With looming petroleum shortages, rare earth magnets are rising as a potential part of alternative energy solutions.
Permanent Magnets
Permanent magnets are objects that have been manufactured from a magnetized material and are thus able to create their own persistent magnetic field. As a whole, magnets can be largely broken up into two categories: non-permanent and permanent.
Non-permanent magnets are electromagnets which require an external electric current to trigger magnetism or non-magnetism. Permanent magnets, on the other hand, retain their magnetism indefinitely or until they are demagnetized by vibration, dirt, corrosion or interfering magnetic fields.
A magnet’s capacity for retaining its magnetism under various conditions is called “magnetic permanence,” and some types of permanent magnets have higher capacities for permanence than others.
Typically, permanent magnets are fabricated from such chemical elements as non-rare earth elements like, alnico (aluminum-nickel-cobalt), ceramics (such as strontium and barium ferrite), and rare earth elements link, Sm-Co (samarium-cobalt) and NdFeB (neodymium-iron-boron). As an advantageous magnet option, permanent magnets are widely used in many industries, particularly for applications which require constant magnetic force, such as in metal separation and holding, as well as the automotive, industrial manufacturing, aerospace, construction industries and more.
In addition to the aforementioned applications, another useful application is that mechanical motion can be created by permanent magnets when an electric current is introduced to one of the magnets’ poles. However, rare earth magnets, including neodymium magnets and samarium cobalt magnets, have a much stronger magnetic force (and higher magnetic permanence) than other permanent magnets and for this reason can be used in small quantities to help with sound amplification and computer data processing.
For instance, very small neodymium magnets help computer hard drives read and store information, or they may cause the vibration in speakers which produces sound. Ceramic magnets and aluminum-nickel-cobalt alloyed alnico magnets, two types of permanent magnet which are fabricated through sintering, are also used to amplify sound as well as for various metal holding, sorting and electric motor applications.
This diversity of applications make permanent magnets essential in food processing, bulk material handling, metal fabrication and handling, electric motor manufacturing, sound amplification, data processing and many other industries. Magnet manufacturers can fabricate custom permanent magnets into a variety of shapes, densities and magnetic strengths.
Rare Earth Magnets
A rare earth magnet is a type of high-strength permanent magnet that is formed from rare earth element alloys, which are derived from a collection of seventeen chemical elements of the periodic table. For applications that require exceptionally strong magnets for holding, separating and lifting, rare earth magnets are by far the most effective type of magnet.
There are two main types of rare earth magnets: neodymium magnets, which are composites of the rare earth element neodymium, iron and boron; and samarium magnets, which are composited from cobalt and rare earth element samarium. Neodymium magnets are both stronger and more affordable than samarium cobalt magnets and are therefore more widely used.
Rare earth elements are also called lanthanoids and are found within certain types of oxide-rich minerals within the Earth’s crust. Lanthanoid elements have partially filled outer f electron shells which are the source of neodymium and samarium’s exceptionally powerful magnetic fields.
The relative scarcity of mineral deposits containing neodymium and samarium combines with the long and costly process of extracting rare earth elements from naturally-occurring ores, making neodymium magnets and samarium cobalt magnets costly in comparison to non-rare earth magnets.
Electro magnets, alnico magnets and ceramic (ferrite) magnets are used extensively in automotive, medical, industrial and aerospace applications; rare earth magnets do the work that weaker ferrite and alnico magnets cannot. Applications for neodymium and samarium magnets are almost limitless, and their functions are often more complex than their weaker relatives.
However, magnetic permanence under conditions such as vibration, corrosion, electric fields and heat is a crucial factor for magnets used in industrial, automotive and medical equipment, and although neodymium composites have good magnetic permanence under most conditions, they lose their magnetism under corrosion and relatively low temperatures (200 degrees Celsius).
In addition, aside from ordinary physical work such as holding, lifting and separating, rare earth magnets are crucial components in electric motors, servo motors, DC brushless motors, wind turbines, TV monitors, welding equipment, power meters, engine timing systems, ignition timing systems, linear actuators, sensors, vending machines and other equipment.
Recently, the rare earth magnet industry has seen a sharp rise since eare earth magnets – mainly neodymium magnets – are crucial in most electric motors, and concern has already been raised regarding lanthanoid ore shortages. With looming petroleum shortages, rare earth magnets are rising as a potential part of alternative energy solutions.
Samarium Cobalt Magnets
With a variety of different styles and types of magnets, it can be hard to settle on the right design for you and your application. Samarium cobalt magnets are one type of magnet, and they fall under the rare earth magnet category.
Often found in applications where high temperatures are a factor, these incredibly strong magnets are second only to neodymium magnets in terms of temperature limits in magnets. In order to know if a rare earth magnet is right for your applications, we encourage you to consult a samarium cobalt magnet manufacturer who will assess your needs and requirements based on your application in order to determine the right magnetic solution for you.
The magnetic force within samarium cobalt magnets is rather strong, as is the case with most rare earth magnets. These magnets are made from a combination of materials and commonly have around 25% to 36% samarium in them. The other materials are mostly two different types of alloys with the first being known as series 1:5 and the second is known as series 1:7.
The series 1:5 magnets have a magnetic strength rating of 16 to 25 MGOe, while series 1:7 has a magnetic strength rating of 20 to 32 MGOe. The way magnetic strength is measured is through the energy in products with units of megagauss-oersteds or MGOe. Samarium cobalt magnets are manufactured through the use of sintering and a series of pressing processes.
The sintering process works to fuse together the tiny particles in the samarium cobalt material while the pressing process can be accomplished in two ways. The first method uses die pressing where pressure is applied from one direction, and the second method uses isostatic pressing where pressure is applied in all directions within a rubber mold.
There are a number of different ways to customize a samarium cobalt magnet. For example, the magnet’s Curie temperature, certain tolerances, and even the magnetic strength can all be modified to fit within the manufacturing process to fit the specific needs of your applications. This is why it is so important to find a trusted, experienced samarium cobalt manufacturer in order to receive a custom solution that is manufactured with your application in mind.
Sheet Magnets
Sheet magnets are large, flat magnets that can be used over large surface areas. A magnet is roughly defined as an object that is surrounded by a magnetic field and that has the property of attracting either iron or steel, and it does not matter if that property is natural or induced. There are a wide range of industries that benefit from the utilization of sheet magnets.
Automotive and consumer industries use sheet magnets, which are fairly flexible magnets, primarily for signage, although there are many other applications. Sold in bulk rolls or cut sheets, sheet magnets consist of two sides, one which is magnetized (the strong side) and the other which is not (the weak side). Since flexible magnets are actually a plastic polymer composite, the lifespan and magnetic force of magnetic sheets are much lower than in other non-polymer magnetic composites.
As a result, sheet magnets are a flexible ferrite-plastic composite which is extruded into magnetic sheets onto which adhesive and/or print is applied. These sheets are then cut to custom shapes and sizes and used for a variety of applications, including refrigerator magnets and displays, magnetic calendars, magnetic business cards, automobile signs and advertisements and many others.
Sheet magnets are available in a wide range of widths, thicknesses and sizes; thicker magnetic sheets have greater magnetic force, since greater magnetic force is contained in greater mass. Due to their flexibility and flat surface, sheet magnets are ideal for advertising and other applications which require large surface areas to hold weak magnetic force.
As a polymer composite, sheet magnets are made of the same material as injection molded and extruded magnets, which are other types of flexible magnets. Injection molded and extruded magnets can be formed, just like plastic, into a virtually limitless range of shapes; the cost of magnetic polymer materials and magnetic polymer extrusions are high, however, and magnetic polymer products have relatively low magnetic force.
For this reason sheet magnets, which are more easily extruded than magnetic polymer shapes, are far more cost effective than any other type of magnet and are by far the most common in consumer industries. To enhance a sheet magnet’s magnetic properties and lifespan, sheet magnets are often laminated on the weak side with a top-coat to keep magnetic properties from seeping out.
The most typical top-coat is vinyl, which is often glossed, colored or printed. Rubber and acrylic are sometimes used to coat magnetic sheets as well.
We are a UK company
Yes, we are a UK company proudly producing and supplying high-quality magnets to customers across the UK and world wide. At Magnosphere, we are offering a wide range of magnets, including powerful neodymium magnets, with fast shipping and excellent customer service. Whether you’re a business looking for bulk orders or an individual in need of specific magnets for a project, we are here to help with expert advice and tailored solutions.
Supplier of Rare Earth Magnet, neodymium magnets and permanent magnets
Our magnetic product assortment includes: disc magnets, ring magnets, magnetic spheres, block magnets, pot magnets, clamping magnets, car roof magnets, ceiling magnets, switching magnets, lifting magnets, flexible rubber magnets, sheet magnets, tape magnets, steel tape, notice boards, notice board magnets, magnetic paper, fridge magnets, business card conversions, magnetic sweepers, magnetic separation rod magnets, separator grids, compasses, gaussmeters, magnetic viewing film, iron filings, experiment kits, generator magnets, reed switch magnets, educational magnets.
We ship our Magnets worldwid via Sea or Air Shipment
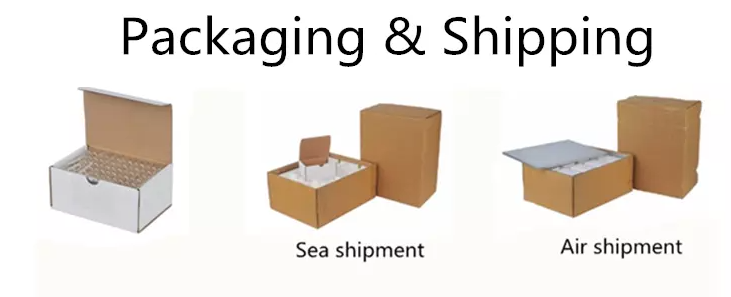
Buy Powerful Neodymium Rare Earth Magnets at Magnosphere and get a better deal!
Magnosphere produces magnets at great prices, produced and delivered on time for all areas of industry, automotive, aerospace, electronics as well as in the design sector, trade fair construction, offices and for the home.
We are an ISO certified shop and carry the Trusted Shops seal. We have successfully completed more than 400,000 orders and offer our ever-growing customer base 24/7 customer service.
All items are available for immediate delivery in large numbers with daily dispatch. Our selection is your win! Thousands of satisfied customers! Buy from a company with the highest quality standards and customer service with flexible and diverse payment options and conditions.
We can also custom manufacture these to fit your exact specifications using our in-house global manufacturing facilities and team of experienced engineers. Need high quantities of magnets at the lowest and fairest price possible? Just let us know what you are looking for and contact our Customer Care Team by sending us a request for quote! We'll work with you to determine the most economical way of providing you with what you need.
Trust in our experience and convince yourself of our service and our products and we look forward to welcoming you to our magnet shop at Magnosphere. You are welcome to contact us by eMail: info(at)magnosphere.uk. Available 24/7 x 365 and we are also there for you on public holidays! Or just give us a call.
ROHS-Directive
Magnosphere conforms to the RoHs directive and the Reach and PFOS regulations. Directive 2002/96 / EC of the European Parliament and of the Council, of January 27, 2003, on waste electrical and electronic equipment (WEEE).

- Hotline:+44 (0)1138683670
- Telefax: +49.2241.9594520
- eMail: info@magnosphere.uk
We are very proud to offer excellent customer service. We know that without our clients, we would not be here. If you have any questions about your order or something else, please call or email us!: info(at)magnosphere.uk
24 / 7 x 365 Including holiday periods! Our customer service team is available to help you!